Monday, February 24, 2014
Wine bottle stoppers 6 and 7
Did two in sycamore today. I know that some wiseguy would say "Why dont you make a wine bottle stopper that looks like a wine bottle?" so thats what I did. As for the other, I thought that it may be important to have some short ones so that if someone wants to put their bottle in a refrigerator, the shorter size will help.

Read More..
Sunday, February 23, 2014
NEW YEAR turquoise cabinet
Here we are in the new year and I find the list of things to do so long.
The holiday decorations now have to come down and be neatly stored away for another year.
We have one of those fancy storage box springs that lift on hydraulics to hide all the Christmas decor.
I recommend these to anyone looking for extra storage.
Kat on the other hand is not so fond of the bed lifting up and disturbing her beauty sleep.
While I work on this list the furniture continues to stack up making
me feel Im not getting much accomplished, and I am disappointed
my reinventing of furniture has not been utilized as much as Id prefer.
So for my first project this year I wanted to get back to creating, recycling, and rebuilding.
I started with a simple vintage 2 drawer chest
A large and heavy framed mirror

Appliques actually salvage road side during last years recycle week

Bits of recycled wood from all my travels including:
stairs spindles, 3 dresser aprons, old pine shelving, and another dresser
of lesser value scarified its self for the structure of the upper portion.
Its painted in a beautiful deep turquoise that has to been seen.
It has been waxed, distressed, and waxed again to a super soft finish.

Sharing with:


![]()

http://diybydesign.blogspot.com/
http://diybydesign.blogspot.com/
Why I train with free weights
I excersize alot but I am not a memeber of a gym or anything like that. I dont want to have to spend the money on a gym membership when I can get a better workout at home.
My older sister has moved out of the house and I now have the upstairs to myself. I have turned her old bedroom into my excersize room, how great! My personal gym consists of; 7 dumbells (2 45lbs, 2 35lbs, 2 10lbs, 1 40lbs), a basic weightbench that can be adjusted to various inclines, a balance ball (the big beachball thing), a pull-up bar that hangs in the door-frame, and an eliptical machine. Other than the eliptical, everything is pretty cheap. The only reason I have the eliptical is because my mother wanted to start excersizing so she bought the eliptical but NEVER even go on it, so I have it now.
With this meager bit of equipment, I think I get a great workout.
Freeweights (dumbells) give you a better workout than the gyms fancy excersize machines. The machines kind of "assist" you in the movements, the guide and balanace the weight. With free weights however, your muscles have to work harder to balance and steady the weight which gives you a much better workout and builds a wider variety of muscles. With machines, specific muscles are targeted rather than a large number of different muscles.
So, if you want to start working out without having to spend much money, then dumbells are definately the way to go!
Read More..
My older sister has moved out of the house and I now have the upstairs to myself. I have turned her old bedroom into my excersize room, how great! My personal gym consists of; 7 dumbells (2 45lbs, 2 35lbs, 2 10lbs, 1 40lbs), a basic weightbench that can be adjusted to various inclines, a balance ball (the big beachball thing), a pull-up bar that hangs in the door-frame, and an eliptical machine. Other than the eliptical, everything is pretty cheap. The only reason I have the eliptical is because my mother wanted to start excersizing so she bought the eliptical but NEVER even go on it, so I have it now.
With this meager bit of equipment, I think I get a great workout.
Freeweights (dumbells) give you a better workout than the gyms fancy excersize machines. The machines kind of "assist" you in the movements, the guide and balanace the weight. With free weights however, your muscles have to work harder to balance and steady the weight which gives you a much better workout and builds a wider variety of muscles. With machines, specific muscles are targeted rather than a large number of different muscles.
So, if you want to start working out without having to spend much money, then dumbells are definately the way to go!
NOUVEAU BROTHERS matching shelf cabinets

The brothers are finished after 10 months.
Yes I started these last October and Ill explain why it took so long very soon.
The upper cabinets have a hinged glass panel with an art nouveau design I hand painted on the glass.

Ill talk about all the details and bits that went into making these beauties next time.
There is still so much gathering and editing of pictures because I used parts from over 8 different
salvaged items to build them.

The color is a creamy white and they have light edge distressing.
The knobs are white ceramic and the legs are cast iron.
Saturday, February 22, 2014
How to Design a Garden Organic Gardening
How to Design a Garden: Organic Gardening
Organic Garden Design

How to Design a Childrens Garden: Organic Gardening
Iicorporate these design

Read More..
Organic Garden Design
How to Design a Childrens Garden: Organic Gardening
Iicorporate these design
Need Help With That First Woodworking Furniture Plan
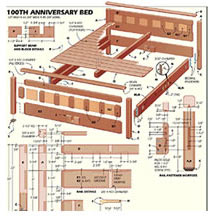
There has never been a better time to find furniture woodworking plans than now. Knowledge is a fingers reach away thanks to the internet. If you are like me and find it hard to get that first project off the ground without some assistance, you can be reassured as I will tell you what has helped me to finish many a project with ease.
Lets be honest, woodworking is a skill that needs to be mastered over many years of practice, but most of us could not afford to put all our effort into it unless it is our full-time work or our hobby. If there is one thing I have learned over time is, in no way be put off by any type of woodworking design. Correct research is a must, so do it right. You will not be stuck for the material you need, because it all can be obtained for free from the library, books, and magazines.
Good plans are the most straight forward ones to follow, which take you through the entire procedure from start to finish. With effective plans you will feel as if you can accomplish any woodworking plan no problems at all. We all have to start off somewhere, and when you come to the end of a design it will give you a sense of extreme satisfaction.
After a few projects underneath your belt, it starts to become easier, and all the things you have learned falls into place. Over time you start to hone your skills, and you can implement these skills to help you tackle your work from different angles. When you have mastered most of the skills necessary, you can take things one step further and put up for sale the merchandise you create, but that is up to you.
As you well know, it can take a lot of time and get-up-and-go on your part to find the right woodworking download before you can commence any work. What would you think if you can go to one place that provides all the teaching you need? It even suggests the best tools for the job, just think about it you have your own instructor with you every step of the way.
I wish this product was around when I was starting out on my woodworking journey. The time and effort not to mention the cash I would have saved. This is one of the best products that I have seen, which helps you through the process. Anyone can implement it. One other outstanding thing about this product, is it caters for all standards of woodworker.
Lets be honest, woodworking is a skill that needs to be mastered over many years of practice, but most of us could not afford to put all our effort into it unless it is our full-time work or our hobby. If there is one thing I have learned over time is, in no way be put off by any type of woodworking design. Correct research is a must, so do it right. You will not be stuck for the material you need, because it all can be obtained for free from the library, books, and magazines.
Good plans are the most straight forward ones to follow, which take you through the entire procedure from start to finish. With effective plans you will feel as if you can accomplish any woodworking plan no problems at all. We all have to start off somewhere, and when you come to the end of a design it will give you a sense of extreme satisfaction.
After a few projects underneath your belt, it starts to become easier, and all the things you have learned falls into place. Over time you start to hone your skills, and you can implement these skills to help you tackle your work from different angles. When you have mastered most of the skills necessary, you can take things one step further and put up for sale the merchandise you create, but that is up to you.
As you well know, it can take a lot of time and get-up-and-go on your part to find the right woodworking download before you can commence any work. What would you think if you can go to one place that provides all the teaching you need? It even suggests the best tools for the job, just think about it you have your own instructor with you every step of the way.
I wish this product was around when I was starting out on my woodworking journey. The time and effort not to mention the cash I would have saved. This is one of the best products that I have seen, which helps you through the process. Anyone can implement it. One other outstanding thing about this product, is it caters for all standards of woodworker.
Friday, February 21, 2014
Sampling The Sector
I dont drink a lot, I dont use any illegal substances, heck most of the time I even drive in the vicinity of the speed limit. I really only have two vices, (the naughty kind, not the attached to my bench kind) that occasionally get in the way of being an attentive husband, father, and employee. One of those is woodworking, the other is studying medieval history.





I gathered from the article that while one sector is functional, a pair of them can be very versatile. One about twice the size of the other. I chose a width for the larger sector and proceeded to rip the width from the narrow stock after marking it out with a marking gauge.

As I worked along I made myself pretty happy, a couple years ago when I started changing my game plan to hand tools theres no way I would have been able to pull off ripping a half inch off a board with a D-7. Now it really didnt seem like a big deal. After sawing I planed the edges first with my #6 for flatness followed by my #3 for smoothness.

Now I had a good ol pair of sticks to make the longer sector.

The shorter sector could be thinner dimensions so I ripped the two sides from one shorter section of stock.

Toplins sector puts the hinges on the endgrain. I know hes probably smarter than me and theres gotta be a reason for it, but I had to go with what felt right to me and that was sinking the screws into side grain. This meant creating a little recess so the hinge will lay flush once installed

Then there comes the knife work breaking the sides into 13 equal sections. I cheated a little and used inch measurements for both sectors, The smaller sector has 13 divisions spaced at an inch and the larger has them at two inches. I measured them out and knifed the lines both on the top, then on the inside of the legs.

A very fine Sharpie pen was put to work darkening all the knife lines.

While I was working away I got to thinking about the layout squares I started building about this time last year and the decorative molding cut outs on the Roubo Square and English Layout Square and how they help make the tool attractive and increase the pleasure I get working with them. I decided to repeat the experience here with these sectors. I cut these ovolo silhouettes on the distal ends of the legs on both pair.

Towards the hinge end of the smaller I rasped out these simple covetto silhouettes.

And the hinge end of the larger sector received this bead detail.

Then came the time to number them one to thirteen. One the smaller I used standard Arabic numerals.

On the larger I decided to change it up and use Roman numerals. No particular reason, a little romance thats all.

Read More..
One of the best things for me is when my two obsessions find common ground, then I can really geek out. this is probably why Ive latched on well to panel carving, Its a drug that feeds both of my obsessions.
One thing I have always wondered about with medieval woodcraft is measuring, before standard empirical measurements. I get the idea of story sticks or string with knots at regular spaces. I understand the concept of measuring by finger, hand, and foot. I also get judging by eye and having a working knowledge of how proportions should work. I have played with all these things but there seemed like there was a missing piece to all of these, and I had my suspicions the mystery was contained in a pair of dividers.
I get the basics of a pair of dividers, transferring measurements and scratching arcs and circles, but I have always suspected that was only scratching the surface. Ive never made it to Woodworking in America, but I know George Walker has taught a class there that connects the use of dividers to design furniture and I wish I could attend for that class most of all. (There are lots of other good reasons I with I could attend)
I am an avid follower of Mr. Walkers blog "Design Matters" blog and I like his articles in Popular Woodworking Magazine and he recently wrote a simple post on a tool rack he built for his shop without using any "measuring" in the sense that we have all been raised to be accustomed to. This connected me to an article written by Jim Toplin (Georges co-conspirator on an upcoming book from Lost Art Press) in the June 2011 issue of Popular Woodworking Magazine called "Secrets Of The Sector."
I dug out my copy of the mag and re-read the article, and Im not sure how I let it slip by me the first time. In the back of my head, everytime I saw a folding rule for sale I would think, "I should pick up a real cheap one I can sand down and convert to a sector" like Chris Schwarz did in this video. But after re-reading the article I couldnt let it pass me by again.
I stopped and picked up a small maple board from the closest box store the next morning. Why maple? It was one of the best bits of stock on the shelf that particular day, and I wanted something light colored and readable when I marked the lines and numbers.
I gathered from the article that while one sector is functional, a pair of them can be very versatile. One about twice the size of the other. I chose a width for the larger sector and proceeded to rip the width from the narrow stock after marking it out with a marking gauge.
As I worked along I made myself pretty happy, a couple years ago when I started changing my game plan to hand tools theres no way I would have been able to pull off ripping a half inch off a board with a D-7. Now it really didnt seem like a big deal. After sawing I planed the edges first with my #6 for flatness followed by my #3 for smoothness.
Now I had a good ol pair of sticks to make the longer sector.
The shorter sector could be thinner dimensions so I ripped the two sides from one shorter section of stock.
Toplins sector puts the hinges on the endgrain. I know hes probably smarter than me and theres gotta be a reason for it, but I had to go with what felt right to me and that was sinking the screws into side grain. This meant creating a little recess so the hinge will lay flush once installed
Then there comes the knife work breaking the sides into 13 equal sections. I cheated a little and used inch measurements for both sectors, The smaller sector has 13 divisions spaced at an inch and the larger has them at two inches. I measured them out and knifed the lines both on the top, then on the inside of the legs.
A very fine Sharpie pen was put to work darkening all the knife lines.
While I was working away I got to thinking about the layout squares I started building about this time last year and the decorative molding cut outs on the Roubo Square and English Layout Square and how they help make the tool attractive and increase the pleasure I get working with them. I decided to repeat the experience here with these sectors. I cut these ovolo silhouettes on the distal ends of the legs on both pair.
Towards the hinge end of the smaller I rasped out these simple covetto silhouettes.
And the hinge end of the larger sector received this bead detail.
Then came the time to number them one to thirteen. One the smaller I used standard Arabic numerals.
On the larger I decided to change it up and use Roman numerals. No particular reason, a little romance thats all.
A quck Danish Oil finish to give them a little protection and when they dry theyll be ready to work. I cannot wait to begin to play with these and explore the possibilities behind them. I know theyre going to help me pull more of the mystery out of using my dividers and Im excited about that. Im going to see how many secrets I can unlock on my own before the Walker / Toplin book arrives on the scene. Im excited to read that too, I hope we dont have to wait to long.
Ratione et Passionis
Oldwolf
For More Info:
Read George Walkers post "Design at the Point of a Tool"
Check out Jim Toplins website.
Chris Schwarz also has a video on using a sector HERE
Working with Partially Decomposed Wood Discussion and Project
Hi Everyone,
Well the sun finally came out today and the temperature has warmed up to a whopping 38 degrees so Im going down to the wood shop-wood turning weather has arrived.
Working with partially decomposed wood
I live in a wooded area that contains a lot of tree limbs and trunks that have either died or fallen as a result of storm or winds. That leaves a lot of potential turning wood laying around that can be used in your projects.
Ive done a very limited number of turnings using this type of wood and Ill share some of my observations with you:

I think if youre careful, this can be a very fruitful source of wood for the more experienced turner.
Small Project-M&M Box
I decided to see how a box would work with a piece of an elm tree that was on my property. I sawed off a 4" piece off the end of a large branch, prepared it for mounting on the lathe and proceeded to turn it.
Ive removed the bark and brushed the surface of the blank. Then I turned the lathe on to about 100 rpm and sanded the surface with a green nylon kitchen scrub pad to remove any dirt and to smooth the surface:

Next I drilled out the center of the box to aid in hollowing it and to establish a depth:

Now Im hand turning the blank. Ill widen the opening and deepen the bowl:

Here is the completed turn.Notice Ive left a thin rim for the lid to sit on. Im going to make this a set in lid:

Next, I cut a small blank out of some scrap red oak and mounted it on the lathe. This became the lid for the box and since it was a thick piece of wood, I was able to cut the knob out of this blank without having to laminate another piece of wood to it:

Here is a photo of the finished lid and the box together:

And this is the finish photo after Ive oiled the lid:

Now that will hold a lot of M&Ms.
The photograph from above is a flower vase that I began before this box and it has a number of problems-oily finish, chewed up end grain. Im going to come back tomorrow and fix those and see how this works out.
Its getting cold and Im going to come it and warm up a bit.
See you tomorrow.
VW
Read More..
Well the sun finally came out today and the temperature has warmed up to a whopping 38 degrees so Im going down to the wood shop-wood turning weather has arrived.
Working with partially decomposed wood
I live in a wooded area that contains a lot of tree limbs and trunks that have either died or fallen as a result of storm or winds. That leaves a lot of potential turning wood laying around that can be used in your projects.
Ive done a very limited number of turnings using this type of wood and Ill share some of my observations with you:
- This wood has been dead for a while and laying out doors in the weather so its partially decomposed. The wood fibers, both visible and invisible, are beginning to break down as the result of the activities of microorganisms and insects. So even though the wood appears solid, it can be fragile. My point here is to treat it as a potential accident waiting to happen. Dont turn this at high rpms, wear lots of protective head and face gear, and if you have a turning cage on your lathe, use it. Dont use badly cracked wood and if you can, use turning tape or duct tape around the blank to keep it intact while its turning.
- The end grain of this wood easily tears, living a pitted surface. Youll need very sharp tools to cut it with and even with sharp tools, its difficult to achieve a smooth surface. Plan on this when youre contemplating designing something out of this type of wood.
- Smoothing the surface of this type of wood can be challenging. Since a lot of the fiber has decomposed away, it tends to have a finely pitted surface. Its difficult to remove turning scratches so turn carefully and slowly.
- Oils dont seem to be the best way to finish this type of wood. The wood is spongy and it tends to absorb the oil unevenly resulting in a muddied finish.

- Im going to experiment with some polyurethane and lacquer and see how this works out.
I think if youre careful, this can be a very fruitful source of wood for the more experienced turner.
Small Project-M&M Box
I decided to see how a box would work with a piece of an elm tree that was on my property. I sawed off a 4" piece off the end of a large branch, prepared it for mounting on the lathe and proceeded to turn it.
Ive removed the bark and brushed the surface of the blank. Then I turned the lathe on to about 100 rpm and sanded the surface with a green nylon kitchen scrub pad to remove any dirt and to smooth the surface:

Next I drilled out the center of the box to aid in hollowing it and to establish a depth:

Now Im hand turning the blank. Ill widen the opening and deepen the bowl:

Here is the completed turn.Notice Ive left a thin rim for the lid to sit on. Im going to make this a set in lid:

Next, I cut a small blank out of some scrap red oak and mounted it on the lathe. This became the lid for the box and since it was a thick piece of wood, I was able to cut the knob out of this blank without having to laminate another piece of wood to it:

Here is a photo of the finished lid and the box together:

And this is the finish photo after Ive oiled the lid:

Now that will hold a lot of M&Ms.
The photograph from above is a flower vase that I began before this box and it has a number of problems-oily finish, chewed up end grain. Im going to come back tomorrow and fix those and see how this works out.
Its getting cold and Im going to come it and warm up a bit.
See you tomorrow.
VW
Labels:
and,
decomposed,
discussion,
partially,
project,
with,
wood,
working
Subscribe to:
Posts (Atom)