Monday, January 27, 2014
Getting Silly
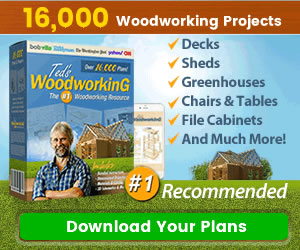
The condo corp decided it was time to change some windows. The crew ripped out the old and popped in the new and did a relatively good job of it. The one thing they didn’t do is replace the inside sills. That would be an improvement of a private residence, and they are not paying for that, so I got stuck with the job.
The original sills were just drywall, prone to the usual cracks, shrinkage and other sundry ailments of plaster in an inconsistent environment. I decided to make the change to oak, now that the opportunity arose.
The last house I built had oversized trim from crown to floor, which was v-groove and pegged, all in oak, and all stained ebony. This ran throughout the entire first floor. Within five years I hated it, but it cost so damned much, I couldn’t bare to rip it down. It may have been the dark stain that I tired of so quickly, but I think it was more the dark slashes and flecks that makes up the harsh grain in oak that got to me the most. That said, this time around only the sills are being done and they will only be varnished.
In my power tool days, lumber was only purchased rough and I would dress it on the jointer and planer. No longer having those tools available to me, I hefted my trusty Stanley No.5, then put it away and headed off to Home Depot to check out the prices. To say I was shocked at what I discovered would be an understatement. Not only was the pricing beyond ridiculous; the wood was junk; warped, twisted, full of knots and good only for firewood. After some hustling, I got a fantastic deal on some great oak, which is now stacked in my livingroom. All I could get was 1” dressed and window aprons were out of the question so I grabbed some 1 x 2, 1 x 4 and 1 x 6.
Today I put together a shorter section to make sure what I had in my head would work attached to the wall.

I cut a 1 x 6 to length and ran my new No.8 over it to make sure it was flat. I did the same to a length of 1 x 2, and when I figured they would match up tight, I glued them together to make the edge appear to be 6/8 stock.

Once glued, I set the Stanley 72 to an eighth and chamfered the lower-front edge, then set it to three-eights and did the same to the top edge.

While this structure is the typical metal studding found in high rises, the single top-plate looks more like a roller coaster track than the base of a window opening. Not only does it rise and fall, but it twists like crazy as well. There is not enough height to add a piece to it to straighten it out so my only choice is to fix the apron solid to the sill and use it as the main connection surface. I’ll just shim the back of it every three feet or so and glue the whole lot in with construction adhesive.

As I could only get 1 x 4 to use for the apron, I had to treat the lower edge and I had just the ticket for this. Last fall, while at the Tools of the Trade show just east of Toronto, I purchased a molding plane from D.S. Orr, yes, the same D.S. Orr that I posted about so disparagingly a couple of months ago. I didn’t know who he was until I spoke to him after those posts. Anyway, H.E. Mitchell made this plane, which is why I bought it. He is really a relatively unknown maker from Brighton, England who operated a shop there in the later half of the 1800’s. I think he is possibly a cousin of my great, great grandfather, and because of that, his wood planes are the only ones I will purchase now. Don’t tell my wife, but I picked up one of his plow planes on eBay the other day. Great stuff!
So with a 1 ½" wood molding plane in my hands, I tackled a 4 piece of oak, cutting a ogee along one edge. A half hour later, I was soaked with sweat, but I had a beautiful edge on that board. Its no wonder men only lived until they were about forty-five or so during the last century. Doing something like this day in and day out would kill ya real quick.

I then quit for the day.
Peace,
Mitchell
Subscribe to:
Post Comments (Atom)
No comments:
Post a Comment